«Производственная система не только для конвейера»
Работа по внедрению отдельных инструментов производственной системы на предприятиях En+ Group ведётся уже давно, однако системный структурированный подход эта деятельность обрела только в текущем году. Так, появилась нормативная база, описывающая и регламентирующая основные направления по внедрению производственной системы, обучения и обмена опытом. Одним из ключевых мероприятий в рамках операционного развития на предприятиях стал управляющий комитет. 5 августа на производственных площадках ООО «Компания «Востсибуголь» и ОАО «ЕвроСибЭнерго» состоялся управляющий комитет по операционному развитию En+ Group.
Связанные одной целью
Главная задача управляющего комитета – знакомство с работой, которая ведётся на предприятиях группы в рамках развития производственной системы, и выявление и распространение лучших наработок. В состав комитета входят члены руководства «En+ менеджмент»: генеральный директор Максим Соков, директор по персоналу Екатерина Никитина, советник по ПС генерального директора КБЭ Александр Моисеев, руководитель проекта Андрей Борисычев, а также представители компаний, входящих в бизнес En+.
Следует отметить, что практика проведения УК также носит системный характер – в нынешнем году это уже второй управляющий комитет, первый прошёл на ООО «КраМЗ» в апреле этого года, а следующий состоится в октябре на предприятиях группы, расположенных в Республике Хакасия. Второй управляющий комитет на своих площадках принимало ОАО «Иркутскэнерго». Совещание состояло из двух самостоятельных блоков. Сначала члены комитета и приглашённые эксперты побывали на Мугунском угольном разрезе в Тулунском районе.
В филиале «Разрез «Тулунуголь» ООО «КВСУ» вниманию членов управляющего комитета были представлены четыре проекта. Необходимо отметить, что у каждого проекта есть своя задача, но вместе они направлены на достижение одной общей цели, стоящей перед компанией, – увеличение добычи на центральном участке с 3,3 до 5 млн тонн угля в год.
Первым проектом, представленным вниманию управляющего комитета, стал проект по повышению производительности бестранспортной вскрыши. Согласно разработанной технологии, для обеспечения добычи 5000 тыс. тонн угля в 2015 году необходимо переместить 21,04 млн кубометров горной массы, из которых 15,04 млн приходятся на бестранспортную вскрышу. «Узким местом» в данной технологии является экскаватор ЭШ-20/90. Анализ текущей ситуации показал, что необходимо повысить производительность данного оборудования на 23,6%. В настоящее время внедрённые в рамках проекта мероприятия уже позволяют достичь годовой производительности на уровне 3,6 млн кубометров. До 2015 года этот показатель необходимо повысить до 3,776 млн кубометров.
Одним из ключевых мероприятий проекта стало формирование транс-портного подуступа для перегона экскаваторов с применением автотранспортной вскрыши. Для обеспечения добычи угля в объёме 5 млн тонн согласно разработанной технологической схеме автовскрышным комплексом необходимо переместить 6 млн кубометров горной массы в год, при этом его текущая производительность 1,422 млн кубометров. Поэтому следующим был представлен проект по повышению производительности автотранспортной вскрыши. Рабочей группе удалось реализовать ряд мероприятий, в результате которых время цикла сократилось с 24 до 23 минут, а производительность увеличилась до 2,11 млн кубометров.
Также в рамках данного проекта участникам управляющего комитета был продемонстрирован новый блок ремонта автосамосвалов. Объект оснащён всем необходимым оборудованием для ремонтов: стендами для ремонта КПП, подвесок, проведения шиномонтажа. Благодаря его строительству появилась отдельная ремонтная бригада из трёх человек, которые были обучены работам по обслуживанию «БелАЗов». Благодаря этому удалось исключить влияние на времяя технического обслуживания погодных условий. В результате время ТО снизилось с 96 до 48 часов, время на монтаж одного колеса – с 3,5 до 1,5 часа.
После того как произведены вскрышные работы и запасы угля подготовлены, необходимо его добыть и вывезти из забоя. Третий проект касается увеличения объёма годовой вывозки угля с центрального блока имеющимся парком оборудования с 3,35 до 5 млн тонн. Чтобы добиться поставленной цели, пришлось на полтора километра приблизить обменный пункт на центральном блоке, а также увеличить с 7 до 9 количество вагонов в составе. Кроме того, переработан регламент по формированию, приёмке и контролю за текущим состоянием железнодорожных тупиков для обеспечения максимального количества вагонов в подаче. Работа над проектом продолжается, так, сейчас усовершенствуется весовое хозяйство – переносятся имеющиеся и устанавливаются дополнительные электронные весы для сокращения маневровых работ при взвешивании. Это позволяет увеличить объём вывозимого угля до 3,64 млн тонн в год.
Залогом успеха этого проекта является бесперебойная работа тепловозов, что невозможно без качественного и своевременного технического обслуживания. Для этого на предприятии строится новое современное депо. В настоящий момент его возведение ещё не закончено, но уже ведётся работа по стандартизации операций. После окончания строительства работа будет продолжена по остальным видам ремонта.
На участках, где реализуются проекты производственной системы, работает большое количество оборудования, и сами участки распределены на большой территории. Поэтому процесс сбора и анализа данных по их работе, анализа результатов реализуемых улучшений очень сложен и трудоёмок. Для решения этой проблемы на предприятии внедряется проект по диспетчеризации системы, которая в режиме реального времени позволяет отследить и проанализировать работу любой единицы техники. Реализация проекта была продемонстрирована членам управляющего комитета.
Руководители других предприятий ООО «Компания «Востсибуголь», принимавшие участие в комитете, продемонстрировали проекты операционного развития, которые они ведут на своих предприятиях в рамках распространения положительного опыта филиала «Разрез «Тулунуголь».
Производственная система по всем фронтам
Тесно связаны между собой и проекты ОАО «Иркутскэнерго», которые были представлены на площадке Ново-Иркутской ТЭЦ. Первый проект «Снижение потерь тепловой энергии при помощи «коротких балансов» направлен на повышение экономической эффективности процесса теплоснабжения потребителей. Добиться этого разработчики проекта предложили за счёт снижения коммерческих и сверхнормативных потерь тепловой энергии и теплоносителя, повышения качества поставляемого энергоресурса потребителям ОАО «Иркутскэнерго».
При реализации проекта одним из ключевых мероприятий стала установка дополнительных счётчиков тепла («кустовых приборов»), что позволило более точно выявлять несанкционированные подключения.
Наряду с несанкционированными подключениями к важным теплопотерям относят утечки, где от скорости реагирования на проблему и качества выполняемых работ зависит количество потерянного теплоносителя. Это послужило предпосылкой для открытия следующего проекта – «Повышение производительности при ремонте тепловых сетей силами персонала ЦОР», целью которого стало снижение затрат на ремонт тепловых сетей. Для этого решено было сократить время ремонта, а сотрудников в высвобожденное рабочее время перенаправить на плановую перекладку тепловых сетей Ново-Иркутской ТЭЦ, чтобы исключить утечки на теплосетях, потери тепла на теплотрассе. Благодаря нововведениям в 2014 году продолжительность ремонта удалось сократить с 30 до 14 дней.
Специалисты на управляющем комитете отметили, что добиться таких хороших результатов без повышения эффективности работы автотранспорта было бы невозможно. Цех организации ремонта, в свою очередь, тоже предложил проект производственной системы, который должен исключить ожидание техники, минимизировать холостые пробеги, снизить затраты на автотранспорт.
Одним из ключевых улучшений стала перевозка угля в ночное время. Это позволило увеличить производительность автомашины в три раза и снизить время доставки угля до котельной в два раза.
В рамках развития производственной системы рабочие группы не только занимаются выявлением и устранением проблем, но и осваивают инновационные технологии. Яркий пример – «Санация магистральных водопроводных сетей НИТЭЦ силами персонала ЦОР». Предпосылкой этого проекта стало большое количество утечек на водоводах «Иркутскэнерго» из-за изношенности сетей. Санация позволяет очистить трубопровод от ржавчины и отложений и нанести на внутренние стенки магистрали цементно-песчаное покрытие толщиной до 10 мм, что продлевает жизнь изношенной трубы более чем на 30 лет. При этом не требуется производить раскопки и нарушать благоустройство, что особенно актуально в свете плотной застройки города. Экономический эффект в 2014 году от использования нового метода восстановления технических характеристик водоводов порядка 7 млн рублей.
Принимающая сторона – Ново-Иркутская ТЭЦ – представила проект повышения эффективности работы ремонтного персонала и вовлечения оперативных сотрудников в выполнение работ по техническому обслуживанию и мелкому ремонту оборудования. Это позволяет разгрузить собственный ремонтный персонал, взять дополнительные объёмы работ, что снизит затраты ремонтного фонда на внешний подряд.
Как пояснили разработчики проекта, снизить трудозатраты собственного ремонтного персонала удаётся с помощью стандартизации рабочих операций. Экономический эффект от реализации данного проекта по итогам 2014 года составит порядка 5 млн рублей. Пример успешной стандартизации рабочей операции также был представлен управляющему комитету. В мастерской по ремонту поверхностей нагрева и арматуры высокого давления участникам показали, что раньше сотрудники тратили рабочее время на ожидание, ненужные передвижения по цеху. После стандартизации всех процессов время проведения ремонта снизилось на 77 минут.
Ломая стереотипы
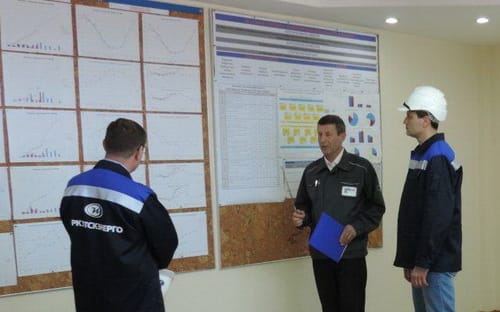
на достижение одной цели
Каждый проект вызвал у членов управляющего комитета интерес. Советник генерального директора компании «Базовый элемент» по производственной системе Александр Моисеев был приятно удивлён уровнем развития производственной системы и количеством открытых проектов в «Иркутскэнерго» и «Востсибугле». Моисеев подчеркнул: крайне важно размещать в комнатах производственного анализа первого и второго уровней логические и визуализированные цепочки «отклонение – выявление проблемы – реализация мероприятий по устранению». Необходимо делать фокус на превентивные ремонты, предупреждение проблем и не только решать вопросы на рабочих местах, но и привлекать другие подразделения, развивать своих поставщиков и подрядчиков. Должны быть чёткие поставленные задачи, важна общая цель для всех, её выполнение, достижение на всех уровнях.
В рамках обсуждения вопроса по обучению ПС директор по персоналу Эн+ менеджмент Екатерина Никитина отметила, что необходимо уделить максимум внимания обучению людей на эталонных участках, для обучения разных уровней персонала использовать различные форматы обучения, систему обучения по ПС необходимо поставить на поток, используя базу корпоративного университета.
Во время обсуждения проблемы падения рабочего напряжения на амперметре ПСУ члены комитета предложили компаниям «Востсибуголь», «En+ логистик» и Ново-Иркутской ТЭЦ разработать совместный проект. Одной из причин выхода из строя оборудования котельного цеха является попадание посторонних механических предметов в подачу сырого угля. Например, в находках нередко встречаются зубья экскаваторов, которые весят до 15 кг. В результате проведённого анализа потока угля от захода на вагоноопрокидыватель до поступления в котёл непосредственно членами управляющего комитета были определены возможные причины попадания посторонних предметов в ПСУ системы пылеприготовления. Рабочая группа проекта в ближайшее время займётся этим вопросом. Кроме этого в ходе обсуждения проблем также было принято решение об открытии ещё нескольких совместных проектов: по ритмичности поставки вагонов и по системе диспетчеризации.
В завершение члены управляющего комитета наметили планы работ. Важным решением было принятие трёхуровневой системы развития ПС (управленческий, инженерный, операционный уровни) за базовую на всех предприятиях En+. Руководитель проекта En+ Андрей Борисычев рассказал, что в формате УК по ПС постарались представить все уровни системного управления. Если в комнате производственного анализа первого уровня были показаны проекты управленческого уровня, то в мастерской по ремонту арматуры ярко представлен операционный уровень.
Также в рамках обсуждения вопроса по обмену положительным опытом Борисычев отметил необходимость создания информационного портала: сайт – важная составляющая развития производственной системы в «Иркутскэнерго». Это позволит развить дух соперничества и предоставит возможность поднять проблему с операционного уровня для принятия управленческого решения. Поэтому одним из приоритетных направлений стала организация информационного ресурса для обмена производственными практиками между филиалами как «Иркутскэнерго», так и всего «ЕвроСибЭнерго».
Очень важные моменты работы «Иркутскэнерго» в целом отметил генеральный директор компании Олег Причко. Он подчеркнул: предприятия «Иркутскэнерго» работают на показателях, не превышающих паспортные, а зачастую и лучше этих показателей, что говорит о хорошей работе всего коллектива. Внедрение инструментов ПС позволяет развиваться, двигаться дальше и оставаться на лидирующих позициях энергетического рынка России. Видеть и решать проблемы по устранению издержек – важный фактор существования эффективной компании.
Итоги второго управляющего комитета по производственной системе подвёл генеральный директор En+ Group Максим Соков. «Происходит разрушение стереотипа «производственная система только для конвейера», мы видим это на примере проектов «Иркутскэнерго» и «Востсибугля». Производственные совещания в подобном формате позволяют нащупать проблемные вопросы не только внутри отдельного бизнеса, но и между бизнесами и определиться с путями их решения. Очень важно, что удалось выявить два потока: управленческий видит системные проблемы и спускает на операционный уровень филиалов задачи по их решению, операционный, в свою очередь, выносит наверх нерешаемые проблемы», – подчеркнул он.